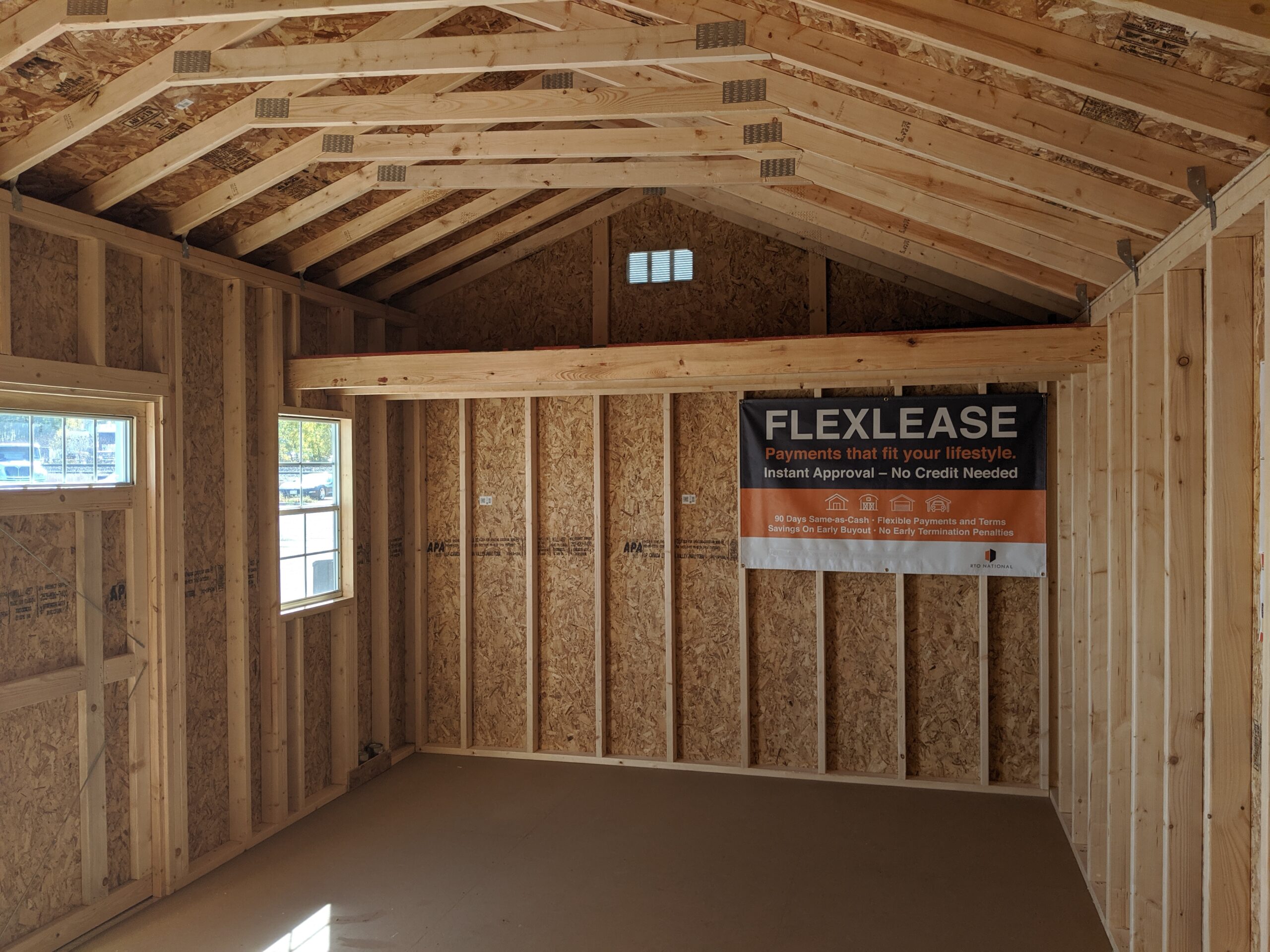
Detailed Plans for a 12x20 Storage Shed with Loft
This document provides comprehensive plans for constructing a 12x20 foot storage shed featuring a usable loft. The design prioritizes functionality, durability, and cost-effectiveness, offering a detailed guide for both experienced builders and those with intermediate DIY skills. Detailed specifications, material lists, and construction steps are provided to ensure a successful project.
I. Foundation and Site Preparation
A solid foundation is crucial for the longevity and stability of any structure. For a 12x20 shed, a concrete slab foundation is recommended for optimal performance. This offers superior resistance to ground movement, moisture, and pests compared to alternative options like gravel pads.
A. Site Selection and Preparation
Before commencing construction, carefully select the shed's location. Consider factors such as:
- Accessibility: Ensure easy access for delivery of materials and future maintenance.
- Sunlight and Drainage: Choose a location with adequate sunlight and proper drainage to prevent water accumulation around the foundation.
- Local Regulations: Check local building codes and zoning regulations for any restrictions or permits required.
- Proximity to Utilities: Avoid placing the shed near underground utilities to prevent accidental damage.
Once the location is finalized, clear the area of vegetation, debris, and any uneven ground. The site must be level for the concrete slab to pour correctly. This may require excavation and compacting of the soil to achieve a stable base.
B. Formwork and Reinforcement
Construct a formwork using pressure-treated lumber to contain the concrete pour. Ensure the formwork is plumb and level, using stakes and bracing for stability. The formwork dimensions should be slightly larger than the shed's footprint to account for the concrete's thickness.
Install a reinforcing mesh within the formwork to enhance the concrete's tensile strength and prevent cracking. This is crucial for a long-lasting foundation capable of supporting the weight of the shed and its contents.
C. Concrete Pour and Curing
Pour the concrete in layers, vibrating it with a concrete vibrator to eliminate air pockets and ensure even consolidation. Level the top surface using a screed and allow sufficient time for curing, typically 2-3 weeks, before proceeding with the shed's construction. Proper curing involves keeping the concrete moist to prevent cracking and ensure optimal strength development.
II. Shed Frame Construction
The shed frame will utilize pressure-treated lumber for its resistance to rot and decay. Accurate measurements and precision cuts are essential for a structurally sound and aesthetically pleasing shed.
A. Floor Framing
Construct a sturdy floor frame using pressure-treated lumber. Employ joists spaced at 16-inch intervals, supported by beams resting on the concrete slab. Ensure proper fastening using galvanized nails or screws. Use a moisture barrier, such as polyethylene sheeting, before installing the floor decking. This will help prevent moisture damage.
B. Wall Framing
Erect the wall frames using 2x4 lumber, following the specified dimensions. Ensure proper bracing and alignment during the framing process. Construct the walls in sections on the ground before raising them and securing them to the floor frame. Install window and door openings according to the design specifications. Proper sheathing is vital for structural integrity and weather resistance.
C. Roof Framing
Construct the roof frame using 2x4 or 2x6 lumber, depending on the desired snow load capacity. The roof design can be either a gable or a shed roof, based on preference and local climate conditions. Ensure proper rafter spacing and support to withstand environmental loads. The roof framing should be properly braced and fastened to the wall frames.
D. Loft Framing
The loft area requires careful planning and framing. Construct supporting beams and joists to create a sturdy platform, ensuring sufficient headroom. Consider the weight capacity of the loft when designing the framing system. Use appropriate fasteners and bracing for a safe and stable loft structure.
III. Exterior Cladding and Roofing
The exterior cladding and roofing are crucial for protecting the shed from the elements. A variety of materials can be used, ranging from affordable options to more aesthetically pleasing and durable choices.
A. Siding
Select the desired siding material, such as vinyl, metal, or wood. Install the siding according to the manufacturer’s instructions, ensuring proper overlapping and sealing to prevent water penetration. Proper installation techniques are essential for a weather-resistant exterior.
B. Roofing
Install the chosen roofing material, which could include asphalt shingles, metal roofing, or other suitable options. Ensure proper underlayment is installed for waterproofing and protection against leaks. The roofing installation must follow the manufacturer’s recommendations and comply with local building codes.
IV. Interior Finishing and Loft Access
The interior finishing touches and loft access creation enhance the functionality and aesthetics of the shed.
A. Interior Walls and Flooring
Consider adding plywood sheathing to the interior walls for added insulation and a cleaner finish. Install appropriate flooring, such as plywood or engineered wood, to create a durable and easy-to-clean floor surface. Consider adding insulation to the walls and roof for better climate control within the shed.
B. Loft Access
Create a safe and convenient access point to the loft. Options include a fixed staircase, a retractable ladder, or a pull-down ladder. Ensure the chosen access method meets safety standards and is easily accessible.
V. Doors and Windows
Install exterior doors and windows, ensuring proper sealing and weather protection. Use high-quality hardware for durability and longevity. Select appropriately sized doors and windows to meet both your functional and aesthetic needs.
VI. Material List (Partial Example)
This is a partial list and should be adjusted based on the specific materials selected and regional pricing.
- Pressure-treated lumber: 4x4 posts, 2x4 studs, 2x6 joists, 2x8 beams
- Concrete: For foundation slab
- Reinforcing mesh: For foundation reinforcement
- Plywood: For sheathing and flooring
- Siding: Vinyl, metal, or wood (specify type and quantity)
- Roofing: Asphalt shingles, metal, etc. (specify type and quantity)
- Doors: Exterior door(s) (specify type and size)
- Windows: (specify type, size, and quantity)
- Fasteners: Nails, screws, bolts
- Insulation: (if desired)
- Paint or stain (optional)
Disclaimer: This document provides general guidance. Always consult local building codes and regulations before commencing construction. This is not a substitute for professional architectural or engineering advice. Seek professional assistance if needed.
No comments:
Post a Comment
Note: Only a member of this blog may post a comment.